From a tradition of six generations of one family comes a modern and innovative, meticulous care and service that the customer needs.
MACHINES OF THE PAST
Simoni’s very first brushmaking machines date back to the middle of the 19th century. These early systems were extremely rudimental, made entirely of wood and, needless to say, entirely hand-operated.
In those years …
|
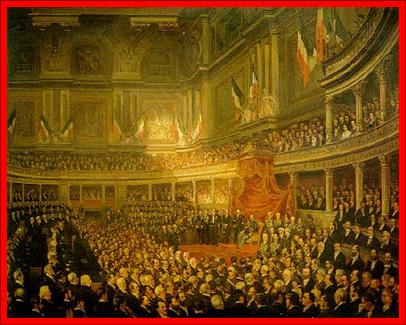 Unification of Italy - The first sitting of Parliament in Turin in 1861
|
The machines presented here are those that we have managed to preserve: they were built between around 1870 and the beginning of the 20th century and were utilised to make various types of brushes and brooms. The brush filaments were hand assembled on pre-drilled wooden laths employing a procedure known as “sewing”. Metal wire or hemp twine was used to fasten the tufts to the wooden lath. This method is still used today when the maximum guarantee of tuft anchorage is required.
In order to date our historic machines spectrometric techniques were used by a specialised laboratory to analyse small samples of wood. This means that the dates are reliable, with tolerance of just a few years each way.
|

Certificate attesting to the spectrometric analysis that allowed us to date the Mazzerini machine at around 1870.
|
MAZZERINI BRUSH MACHINE
The “Mazzerino” is a traditional biconical brush made of couch-grass (a vegetable root) tied with wire or hemp twine. These brushes were mainly employed in the kitchen to clean tableware and cooking utensils.
The machine is composed of a bench, a reel for the metal wire, and a reel brake. The operator would grasp the couch-grass and bind it with the wire before releasing the brake to make another “mazzerino” brush - approx. 1870.
|
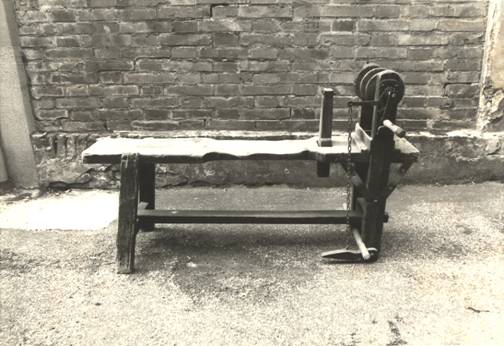 |
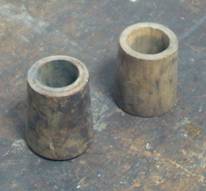 Boxwood bearings |
BORING MACHINE
This machine was used to drill conical thru-holes in the wooden laths so that the filaments could be sewn into them.
The boring tools were handforged in a spoon shape. The tools were mounted on the spindle, which was driven by a waterwheel via a leather belt transmission. The height of the spindle crossbar was adjustable by means of wooden screws.
The pedal control left the operator’s hands free for higher productivity.
The boring machine spindle generally ran in bearings made of boxwood, renowned for its hardness - approximately 1880.
|
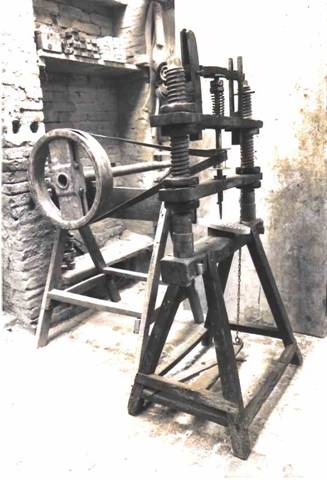 |
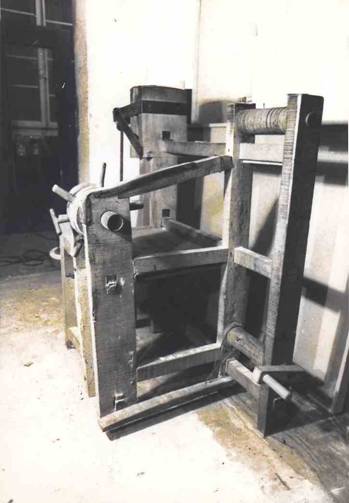 |
BROOM MAKING MACHINE
The boss with an axial bore was used to insert the broom handle so that the sorghum (vegetable fibre) could be bound to it with wire. A specially shaped vice was utilised to impart the classic fan shape to the broom. Once it has assumed this position the broom was fastened by sewing the sorghum using large forged awls.
VICE
The vice is made entirely of wood, including the large diameter screw. The vice was used mainly for gluing of wood laths, for grinding tools, and for carding horsehair.
|
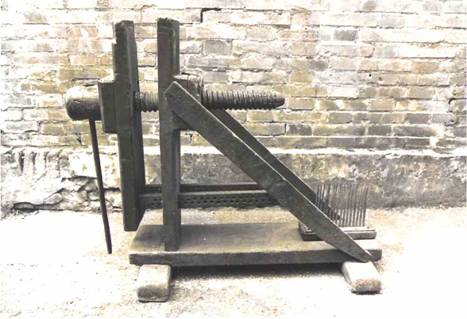 |
This coarse-toothed iron comb was used to prepare the vegetable fibres before sewing them to the lath.
|
|
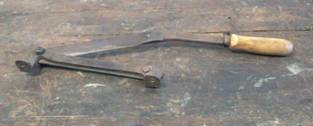 This shear was used to cut bunches of filaments and also to trim the brushes. After sewing, each individual row of tufts was cut to measure with the shear.
|
|
AWLS
For more refined brushes, such as clothes or hair brushes, the tufts where attached by stapling into the lath rather than being fixed with thru-holes. This was performed using a special type of awl in a technique known as ‘crochet’ – approximately 1920.
|
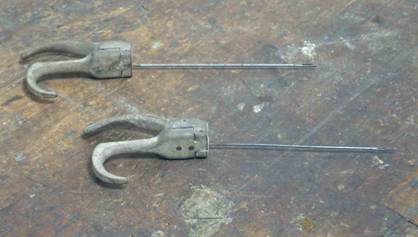 |
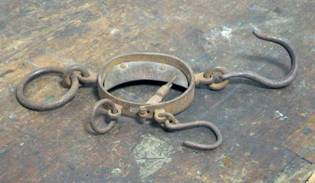 Strain gauge, utilised as a scale for weights of up to 150 kg.
|
|
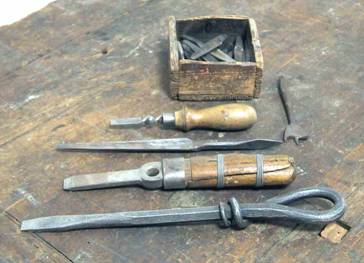 All tools were hand forged, from screwdrivers to gouges and drill bits. The drill bits of the time feature a conical spoon shape. The square section shank facilitated drive transmission by the spindle.
|